La quatrième révolution industrielle a fait basculer l’industrie dans le mode 4.0. Grâce au Big Data et aux nombreux capteurs présents sur les process de production, les objectifs de croissance et de compétitivité de votre entreprise seront améliorés. L’historisation des données dans l’industrie 4.0 est l’un des leviers pour atteindre ses objectifs de croissance.
🤔 Mais en quoi consiste cette historisation et quels sont ses avantages ?
En quoi consiste l’historisation de données temps réel dans l’industrie 4.0 ?
L’historisation de données consiste à collecter, stocker et analyser des données sur une période de temps prolongée. Cette pratique permet de suivre l’évolution d’un phénomène. Elle vise à mieux comprendre les tendances et les modèles qui sous-tendent cette évolution.
Les données historisées peuvent être analysées de différentes manières, en utilisant des outils statistiques ou des logiciels de gestion de données. De plus, vous pouvez les visualiser sous forme de graphiques ou de tableaux de bord pour en faciliter la compréhension à travers des IHM.
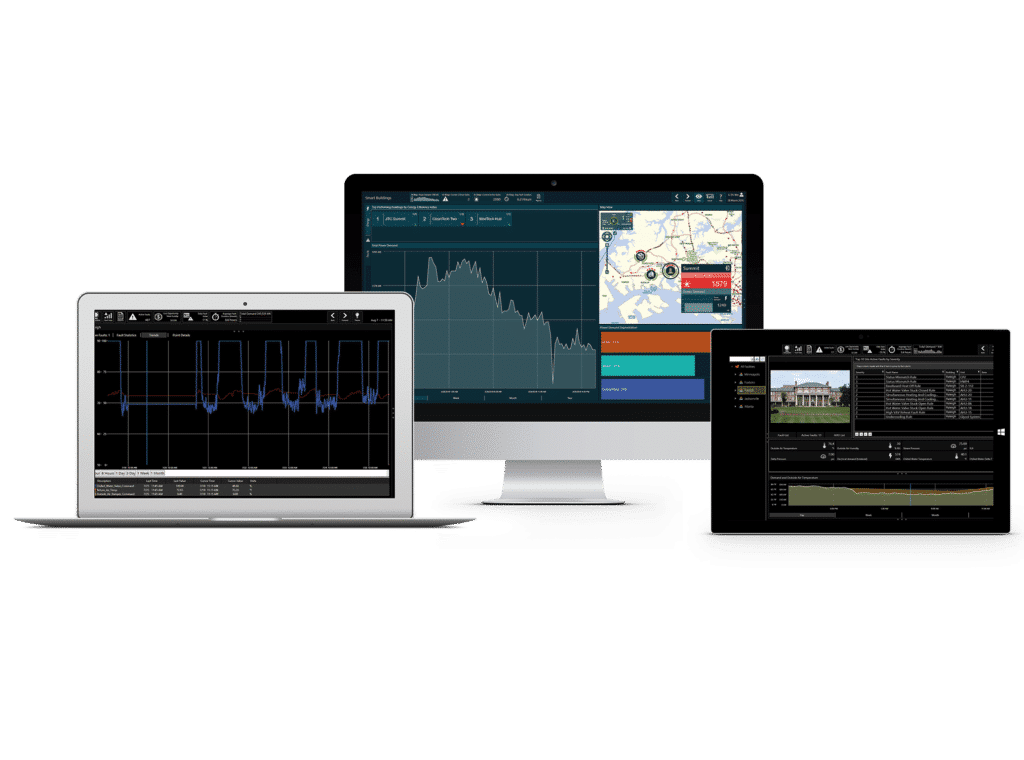
Les avantages de l’historisation de données temps réel dans l’industrie 4.0
L’historisation de données est particulièrement utilisée dans les activités de gestion de la production d’usine et de maintenance. Elle permet d’améliorer l’efficacité et la performance des entreprises. Dans ce but, elle leur donne la marche à suivre pour prendre des décisions éclairées et de mettre en place des actions correctives ciblées.
ETAPE 1 : La collecte des écarts de qualité des process de production
Les données temps réel sont collectées quelle que soit la source de laquelle elles proviennent. Appareils connectés ou matériels anciens, toutes les données sont analysées.
Pour améliorer la qualité des produits, le suivi des paramètres de production permet de détecter les écarts de qualité. L’objectif est d’améliorer les process de production de l’entreprise ou de l’usine. Par ailleurs, l’identification des tendances concernant les pannes et les problèmes récurrents permet de les prévenir.
ETAPE 2 : Identifier les tendances en donnant du sens aux données
L’analyse des données historiques vise à repérer les tendances et les patterns dans les processus de production. En comparant les données réelles aux données cibles, il est possible d’y repérer les problèmes et les anomalies de fabrication.
ETAPE 3 : Optimiser et partager les paramètres process pour suivre les performances
Les solutions de mise en forme et de partage des données temps réel sont simplifiées avec le client pour l’optimisation de la production.
En enregistrant les données relatives aux performances des machines et des acteurs, il est aisé de les suivre. La prévisibilité peut également être améliorée. Il est en effet possible de prévoir les futurs besoins en matières premières, en main-d’œuvre, les délais de fabrication et les coûts. C’est pourquoi l’optimisation des paramètres pour les futurs processus de production se fonde sur la connaissance des paramètres de production utilisés dans le passé.
ETAPE 4 : Des solutions de visualisation du suivi de maintenance de chaque process
Des tableaux de bord ou des tableaux de données Excel sont facilement réalisables à partir des données brutes, sans compétences d’expert. L’historisation des données permet ainsi de suivre les données relatives à la maintenance des machines et des équipements. L’analyse s’effectue en temps réel sur une période donnée.
L’identification des problèmes et des opportunités d’optimisation présente plusieurs avantages.
- Premièrement, Planifier la maintenance préventive grâce aux données relatives aux heures de fonctionnement, aux cycles de production et aux pannes.
- Deuxièmement, Suivre les performances en enregistrant les données relatives aux machines et équipements. La prise de décisions de transformation est ainsi améliorée.
L’objectif visé est d’améliorer l’efficacité et les coûts de la maintenance préventive. Grâce à une vision sur ses historiques, le choix des meilleures pièces de rechange est facilité. Ainsi, des informations sur les meilleurs prestataires sont disponibles pour optimiser les coûts et les temps d’arrêt.
ETAPE 5 : Des données qui facilitent la prise de décisions et améliorent les processus
Le fait de collecter, stocker et analyser des données en temps réel permet d’améliorer les process de fabrication. Ainsi, il est possible de prendre de meilleures décisions stratégiques, en vue de la satisfaction client. L’enregistrement des informations relatives à la production sur une période donnée permet de développer une intelligence opérationnelle.
Quel outil pour créer votre big data industriel ?
Le panorama des solutions d’historisation de données est large. Le logiciel Hyper Historian d’ICONICS permet l’historisation des données de production et de maintenance. Il est capable de collecter les données des capteurs industriels des entreprises de l’industrie 4.0.
Il est conçu pour :
- collecter, stocker et afficher l’information et les données en temps réel ;
- les analyser pour identifier les tendances et les anomalies ;
- générer des rapports pour les indicateurs clés de performance (KPI) ;
- visualiser des données en mode graphique, tableau de bord et histogramme.
Le logiciel Hyper Historian est compatible avec une grande variété d’applications de communication industrielles (OPC, Modbus, etc.). Il s’intègre en toute sécurité aux systèmes de supervision et d’automatisation existants.
Pour conclure, si vous recherchez une solution efficace, le logiciel Hyper Historian constitue une application de choix pour votre système. Elle améliorera la productivité de vos lignes de production et votre maintenance en utilisant vos données historiques. Ainsi, votre entreprise réduira ses coûts, facilitera le contrôle qualité de ses produits et augmentera l’efficacité de sa maintenance.
Demandez une démo dès aujourd’hui !